You may be wondering whether to buy a wet blast or dry blast cabinet. Both have advantages and disadvantages. Let’s look at each type of blast cabinet, and what type of sandblasting jobs each one is best suited towards.
Dry Blast Cabinets
The most common type of abrasive blasting cabinet is a dry blast cabinet. Typically, dry blast cabinets will either operate on a siphon system or using direct pressure via a pressurized vessel (aka a pressure pot or blast pot).
With dry blasting, it is important to match the right air compressor and dust collector to your cabinet size. This is because dry blast cabinets produce dust, both from the surface being blasted, and the abrasive media being eroded as it impacts the surface.
Dry blast cabinets cost a bit less to get started with, when compared with a comparable wet blast cabinet. Another advantage of dry blast cabinets is that you can use a wide range of blast nozzle sizes, so long as you have an adequate compressed air source.
Wet Blast Cabinets
Traditionally, wet blast cabinets have used a slurry blast system. However, our wet blast cabinet, the Vapor Blast Cabinet RB3630S, combines the capability of outdoor direct pressure wet blasting, and puts that inside of a cabinet.
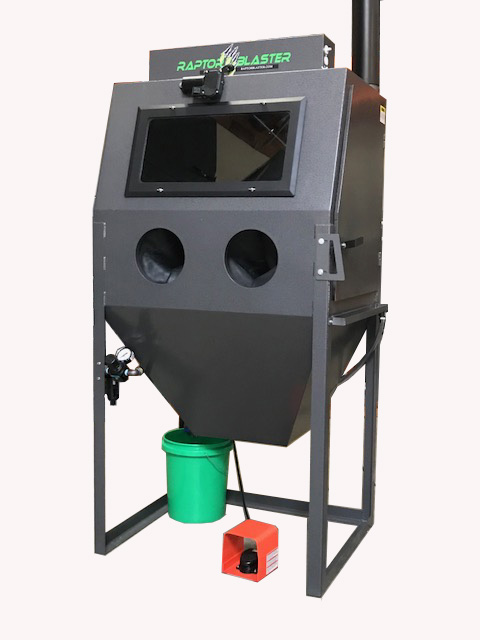
Why is wet blasting preferred for certain applications? Wet blasting produces no dust, which is why it is also known as dustless blasting. For wet blast cabinets, you will need a mist collector instead of a dust collector, to maintain visibility inside the blasting cabinet.
Though wet blast cabinets are more expensive to get started with as opposed to dry blast cabinets, there are some distinct advantages to wet blasting.
When using a dry blast cabinet, the blasting surface produces frictional heat, from the blast media striking the surface. Wet blasting cabinets produce significantly less frictional heat than dry blasting, as the water cools the surface. For delicate blasting jobs, a wet blast cabinet may be the best choice. Wet blasting also is the way to go if you want to avoid any media particulates being embedded in the blasted surface. Aircraft parts and aerospace applications are two instances where wet blasting may be preferred.
One disadvantage with wet blast cabinets is the increased chance of flash rust contamination. This is when you remove rust or other coating from a metal surface. Because water is part of wet blasting, you will need to use a rust inhibitor right after wet blasting. Whereas with a dry blast cabinet, you have a longer window of time to apply rust inhibitor to the blasted surface.
An advantage that a wet blast cabinet has over a dry blast cabinet is that the cleaning step is usually taken care of. Wet blasting may also take less media to strip and clean a surface for a comparable job compared to a dry blast cabinet.
In Conclusion
Every production shop has different needs. If you have more questions about whether you should buy a wet blast or dry blast cabinet, reach out to us via our contact form.