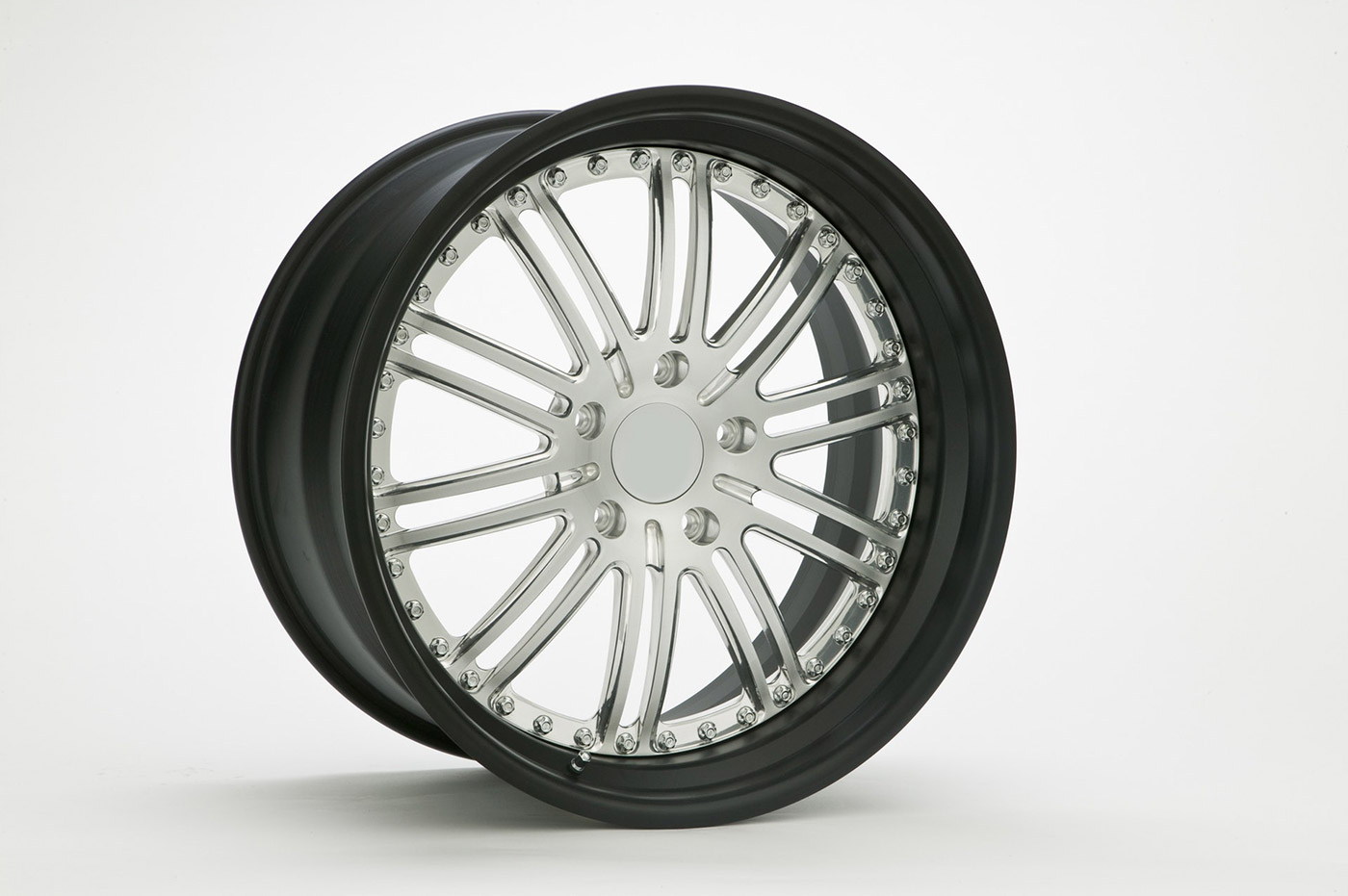
There are many reasons you may want to sandblast aluminum wheels.
Some of you may want to remove the factory paint or primer. Perhaps you wish to remove corrosion or grime. Maybe you are going to re-paint or powder coat the wheels. You may even want to get down to the plain metal surface and polish up the wheels.
This guide will help you effectively blast aluminum surfaces of all varieties.
Methodology
The traditional method for blasting aluminum surfaces is to dry blast, and then polish the surface. After this, the surface can be painted or coated. This works for larger surfaces like an automobile, or a boat hull. Outdoor blasting is generally done with a pressure pot sandblaster.
For smaller objects, like aluminum wheels, rims, or parts, a more efficient method now exists.
By using a vapor blast cabinet, or a slurry blasting cabinet, the blasting time is greatly reduced, and the polishing step is eliminated completely. The advantage of wet blasting is that it produces no dust. With a slurry blast cabinet, the media and water are mixed, then blasted at the surface. With our Vapor King, we’ve combined the force of direct pressure blasting with wet blasting. Both options make stripping a surface much quicker than the old dry blast and polish methodology.
Wet Blasting Aluminum vs Dry Blasting Aluminum
The biggest advantage of wet blasting aluminum wheels and surfaces is that the prep time is much less than with dry blasting. Conversely, the biggest disadvantage with wet blasting is that you’ll have to coat the blasted surface more quickly than with dry blasting. Wet blasting eliminates a lot of the embedded media particles that you find with dry blasting, but painting or coating should be done quickly to eliminate any chances of oxidation.
Choosing the Right Blast Media
If you are blasting aluminum surfaces, the abrasive media most often used is glass beads, sodium bicarbonate, or walnut shells.
Steel shot or steel grit should be avoided. Steel is harder than aluminum, and can create a surface profile, which leads to corrosion.
If you are stripping aluminum wheels to add paint or powder coating, aluminum oxide or crushed glass are good choices. These will leave a anchor profile, which will allow the new coating to grip to the aluminum substrate.
If the goal is to strip an aluminum surface to achieve a polished look, glass beads or soda will be your best choice. If you dry blast, you may still need to polish the surface after the blasting is finished.
Sandblasting Pressure for Aluminum Surfaces
Some aluminum surfaces have thinner panels than other materials. To avoid warping during abrasive blasting, start with a relatively low pressure, 50 to 60 PSI, and increase as needed. For contained blasting, like in an abrasive blast cabinet, the size of the cabinet and blast nozzle will affect how much PSI you need to use.
The larger the blast nozzle, the more air pressure you will need to effectively blast. You can find a handy reference chart of recommended CFM here.
Test a Small Section of the Surface First
Start by testing a portion of the blasted surface. If the air pressure and results look good, feel free to blast the rest of the surface suing the same conditions.
Final Thoughts
Depending on what type of aluminum surfaces you will be blasting, and how frequently, there are different types of equipment you should use. For large surfaces, like an automobile exterior or a ship hull, an outdoor pressure pot sandblaster may be the best fit. For objects like rims or wheels, a dry blast cabinet or slurry blast cabinet is an excellent choice.